반도체 공정 장비에서는 진공 유지, 오염 차단, 공정 신뢰성 확보를 위해 O-Ring을 이용한 정적(Static) 씰링 구조를 광범위하게 사용한다. 특히 플라즈마, 고온, 케미컬 환경에 노출되는 장비에서는 O-Ring Groove(홈)의 정밀한 설계가 장비 성능과 유지보수 주기에 결정적 영향을 미친다.
이 글에서는 반도체 장비용 O-Ring Groove 설계에 필요한 핵심 기준을 총정리한다.
1. O-Ring Groove의 역할
- 진공/대기 분리: 외부 공기나 오염 입자의 유입 차단
- 기밀 유지: 공정 챔버 내 고진공 조건 안정화
- 오링 고정: 조립 중 이탈 방지 및 씰링력 유지
2. 주요 설계 기준
2.1 압축률 (Compression Ratio)
- O-Ring을 눌러주기 위한 깊이 조절 항목
- 정적 씰 기준: 20% ~ 30% 권장
- 과도한 압축 → 재질 손상
- 부족한 압축 → 진공 누설 발생
- 고온에서 사용할 경우, 상온에서는 20%에 가깝게, 운전온도에서는 30%를 넘지 않게 조절 필요.
2.2 Groove 형상
반도체 장비에서는 O-Ring의 고정성과 조립성을 고려해 아래 3가지 형상을 선택적으로 사용한다.
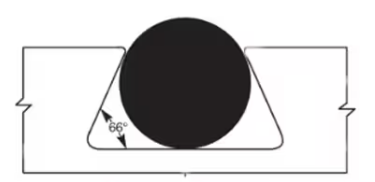
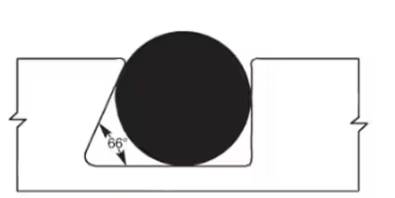
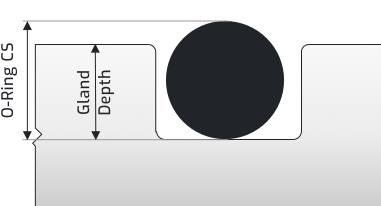
형상 | 특징 |
Rectangular | 가장 일반적, 가공과 조립이 쉬움 |
Half Dovetail | O-Ring 탈락 방지에 유리, 수직 체결 구조에 적합 |
Dovetail | O-Ring을 완전히 고정, 진동/고진공 환경에 적합하지만 가공 및 조립 난이도 높음 |
- 밑면이 넓은 Half 및 Dovetail 오링 그루브는 공구의 진출입을 위한 Hole이 필요
- 이 Hole은 오링빼기 홈으로도 사용됨.
- 그러나 공구 진출입 hole의 날카로운 부분은 오링 손상을 줄 수 있어 특수 공구를 통해 공구 진출입 hole 없이 가공하는 경우도 있음.
2.3 Groove Fill (충전률)
- O-Ring이 Groove 내에서 차지하는 체적 비율
- 권장 범위: 70% ~ 90%
- 과도한 Fill → 과압착, 돌출, 손상
- 부족한 Fill → 씰 압력 불균형 및 누설 위험
- 고온에서 사용할 경우, 운전온도에서 열팽창 고려 필요.
2.4 표면 조도 (Surface Finish)
- Groove 접촉면 조도는 Ra 0.4 µm 이하 권장
- 너무 거칠면 O-Ring 표면 손상 및 리크 유발
- 너무 매끄러운 경우 정적 씰 기준으로는 큰 문제 없음
2.5 O-Ring Stretch (신율)
- 조립 시 O-Ring을 끼우기 위해 늘어나는 비율
- 내경 기준 Stretch 권장 범위: 1% ~ 3% (최대 5% 이하)
- 과도한 신율은 조립 난이도 증가, 단면 변화, 장기 피로 손상 초래
- 특히 FFKM 재질은 Stretch에 민감
3. 최종 요약 체크리스트
압축률 | 20 ~ 30% |
Groove Fill | 70 ~ 90% |
Stretch (신율) | 1 ~ 3% (최대 5%) |
Groove 형상 | Rectangular / Half Dovetail / Dovetail |
표면 조도 | Ra 0.4 µm 이하 |
재질 선택 | 공정 환경에 맞춰 선정 (FKM, FFKM, EPDM 등) |
결론
반도체 장비에서 O-Ring Groove 설계는 단순한 치수 설계를 넘어서 정밀한 밀봉 성능, 장기 신뢰성, 공정 적합성을 확보해야 하는 고난이도 설계 요소다. 압축률, Groove Fill, Stretch, Groove 형상 등을 종합 고려해 최적의 씰링 구조를 구현하는 것이 장비의 수명과 성능에 직접 연결된다.
'기구설계 > 요소설계' 카테고리의 다른 글
O-ring: 반도체 및 진공 장비용 오링의 이해 (0) | 2025.04.05 |
---|---|
Lok 피팅 - 조립 시 토크와 회전 각도 가이드 (0) | 2025.04.05 |
Lok 피팅이란? (0) | 2025.04.05 |
VCR 피팅 완전 정리 – 초정밀 금속 씰링과 고압·고진공 대응 (0) | 2024.06.12 |
관용 테이퍼 나사 완전 정리: PT(R) vs NPT (0) | 2024.06.11 |